Head of Laboratory
Korsunsky, Alexander M
Publications
559
Citations
10 089
h-index
51
Authorization required.
Multi-laboratory collaborative research
Research directions
Residual stress across the scales
+
Publications and patents
Lab address
Wellington Square, Oxford OX1 2JD, United Kingdom
Authorization required.












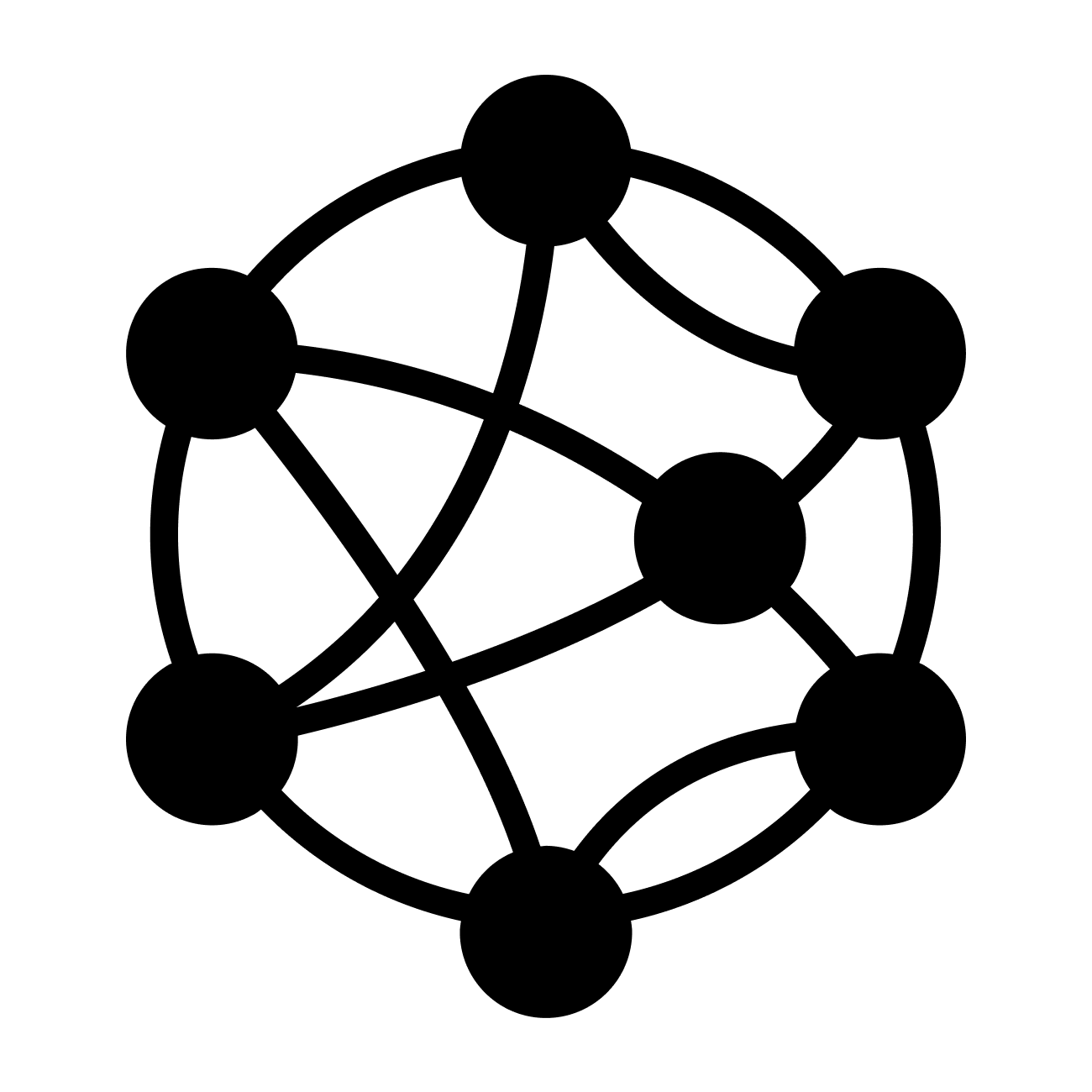