Pirogova, Yulia Vyacheslavovna
Publications
6
Citations
33
h-index
4
Nothing found, try to update filter.
Tashkinov M., Pirogova Y., Kononov E., Shalimov A., Silberschmidt V.V.
Generative adversarial neural networks with a variational autoencoder (VAE-GANs) are actively used in the field of materials design. The synthesis of random structures with nonrepeated geometry and predetermined mechanical properties is important for solving various practical problems. Geometric parameters of such artificially generated random structures can vary within certain limits compared to the training dataset, causing unpredicted fluctuations in their resulting mechanical response. This study investigates the statistical variability of mechanical and morphological characteristics of random 3D models reconstructed from 2D images using a VAE-GAN neural network. A combined multitool method employing different mathematical and statistical instruments for comparison of the reconstructed models with their corresponding originals is proposed. It includes the analysis of statistical distributions of elastic properties, morphometric parameters, and stress values. The neural network was trained on two datasets, containing models created based on Gaussian random fields. Statistical fluctuations of the mechanical and morphological parameters of the reconstructed models are analyzed. The deviation of the effective elastic modulus of the reconstructed models from that of the original ones was less than 5.7% on average. The difference between the median values of ligament thickness and distance between ligaments ranged from 3.6 to 6.5% and 2.6 to 5.2%, respectively. The median value of the surface area of the reconstructed geometries was 4.6–8.1% higher compared to the original models. It is thus shown that mechanical properties of the NN-generated structures retain the statistical variability of the corresponding originals, while the variability of the morphology is highly affected by the training set and does not depend on the configuration of the input 2D image.
Pirogova Y., Tashkinov M., Vindokurov I., Silberschmidt V.V.
This paper studies the effect of different combinations of morphological parameters of porous closed-cell materials on their elastic properties and mechanical behaviour. Three-dimensional representative volumes of porous media with different polyhedral void shapes are investigated, considering variation of statistical realisations of morphological features, such as shape, size and distribution of pores. Description of morphology of each investigated representative volume is formalized using second- and fourth-order correlation functions. The effective properties of representative volumes are calculated with finite-element analysis. Additionally, samples of the studied models were additively manufactured with polystyrene, using fused filament fabrication (FFF/FDM) 3D-printing technique, and subjected to compression. Experimental results for elastic mechanical properties and distributions of strain fields on the surface of the samples, obtained with micro-DIC (digital image correlation), are compared with results of numerical finite-element computations. This is accompanied by analysis of internal-stress distributions to assess the mechanical state of the structures. Patterns and trends observed in mechanical responses of porous materials depending on their different morphological parameters are outlined and discussed.
Vindokurov I., Pirogova Y., Tashkinov M., Silberschmidt V.V.
Understanding the mechanical behaviour of additively manufactured (AM) biomedical polymeric devices under various loading regimes is important for tailoring their design to specific applications. This paper presents the results of an experimental study of compressive mechanical properties of AM cubic samples of biocompatible polylactic acid (PLA) manufactured with fused filament fabrication. The measured elastic modulus and ultimate compression strength were compared and analysed for varying testing parameters, such as strain rate and contact friction, for samples with different characteristic sizes. The changes in density of the samples were also assessed for evaluation of the extent of material compaction after deformation. Surface morphology of specimens was examined before and after compression tests using scanning electron and optical microscopy. Different types of defects induced by the manufacturing process and caused by the subsequent compressive deformation were studied and compared. The obtained results are useful for design and optimization of small-size biomedical devices, which require precise control of their structural morphology and mechanical behaviour.
Elenskaya N., Tashkinov M., Vindokurov I., Pirogova Y., Silberschmidt V.V.
Applications of additive manufacturing (AM) in tissue engineering develop rapidly. AM offers layer-by-layer creation of complex objects, developed to restore functionality of, or replace, damaged tissues. Porous 3D-printed functional gradient structures are of particular interest: their special architecture makes it possible to simulate the heterogeneity of the replaced tissue and, by continuously changing the mechanical properties, to avoid the concentration of stresses that can be caused by abrupt geometric changes. Such structures also allow combinations of different types of unit cells and a smooth transition between them, making design of personalised scaffolds with optimal parameters for the replacement of damaged host tissue at the interface between tissues possible. This paper presents the results of development of scaffold structures with gradients of porosity and multi-morphology using unit cells based on triply periodic minimal surfaces (TPMS). The mechanical behaviour of additively manufactured scaffold prototypes made of polylactide acid (PLA) was studied under compressive loading. Strain fields on their surface were captured using the Vic-3d Micro-DIC digital image correlation system and compared with those obtained with detailed numerical simulations, employing elastic-plastic properties of PLA, obtained in experiments. The effect of gradient parameters and unit-cell morphology on the stress distribution in scaffolds was analysed. A smooth gradient transition between cells with different morphologies was found to reduce the probability of structural failure under intense compressive loading. A good agreement between numerical results and experimental data was achieved, which justifies application of the developed approach to design of personalised bone scaffolds.
Vindokurov I., Pirogova Y., Tashkinov M., Silberschmidt V.V.
This work presents the results of an experimental investigation of the mechanical properties of polyetheretherketone (PEEK) specimens additively manufactured (AM) by using fused filament fabrication with different printing parameters and subjected to postprocessing heat treatment. Standard and compact tension samples were manufactured with a different infill angle using 0.4 mm and 0.6 mm nozzle diameters. Some of the samples were subjected to heat treatment at 220 °C after manufacturing. Tensile tests were conducted to determine the values of elastic modulus, tensile strength, as well as mode-I fracture toughness and critical strain energy release rate. Tensile properties of single-thread and as-delivered filaments were also studied. It was concluded that heat treatment significantly improved the elastic properties, tensile strength and fracture toughness of the AM PEEK samples: the fracture resistance increased by 33 to 45% depending on the stacking order, while the tensile strength increased by some 45–65%, with the elasticity modulus grown by up to 20%. Strain fields induced in specimens by crack propagation were captured with a digital image correlation technique and compared with results of numerical simulations implemented with the extended finite-element method (XFEM). Conclusions on the optimal parameters of 3D printing of PEEK were made.
Pirogova Y., Tashkinov M.
The aim of this work is to investigate the influence of the shape of voids in porous 3D printed closed-cell porous structures on their elastic properties and mechanical behavior using the results of morphological analysis of microstructure based on multipoint statistical characterization, finite element modelling and experimental data. The geometrical models of representative volume elements (RVEs) for structures with non-overlapping inclusions of different shapes and parameters were created and produced using FDM/FFF 3D printing technology. Evaluation of various morphological parameters has been performed based on the analysis of multipoint statistical characteristics. The elastic behavior and properties of the studied RVEs were modelled using finite element analysis. The relationship between mechanical properties and statistical characteristics has been analyzed.
Nothing found, try to update filter.
R N.J., Aravind Raj S.
Abstract
Additive manufacturing has transformed the production of complex and tailored components in multiple industries, including aerospace, automotive, biomedical, and consumer products. Nonetheless, maintaining the quality and reliability of these components presents a significant challenge. This review paper examines the progress made in quality control methodologies specifically designed for additive manufacturing processes. Conventional quality assurance techniques, including dimensional measurement, visual assessment, and mechanical evaluations (such as tensile, compression, and impact testing), are essential for determining the quality of the final component. Nonetheless, these techniques might not adequately identify internal flaws. This review analyzes the increasing importance of non-destructive testing (NDT) methods, including ultrasonic testing, computed tomography (CT), and infrared thermography, in detecting internal defects such as porosity, cracks, and lack of fusion. The document examines the foundational principles of these NDT techniques, evaluates their benefits and drawbacks within the framework of additive manufacturing, and underscores the latest developments in their utilization. Additionally, the analysis highlights the critical role of in-process monitoring and real-time quality assurance techniques. These methods focus on identifying and rectifying flaws during the printing process, thereby reducing the likelihood of generating defective components. This detailed analysis offers an in-depth examination of the present advancements in additive manufacturing quality control, emphasizing the essential contributions of both conventional and innovative methods. By analyzing the strengths and limitations of these methods, researchers and industry professionals can create more robust and effective quality control strategies, ultimately resulting in the production of high-quality and reliable AM components.
Turker B.
Fused Deposition Modeling (FDM) is a prominent additive manufacturing technique known for its ability to provide cost-effective and fast printing solutions. FDM enables the production of computer-aided 3D designs as solid objects at macro scales with high-precision alignment while sacrificing excellent surface smoothness compared to other 3D printing techniques such as SLA (Stereolithography) and SLS (Selective Laser Sintering). Electro-Spinning (ES) is another technique for producing soft-structured nonwoven micro-scale materials, such as nanofibers. However, compared to the FDM technique, it has limited accuracy and sensitivity regarding high-precision alignment. The need for high-precision alignment of micro-scaled soft structures during the printing process raises the question of whether FDM and ES techniques can be combined. Today, the printing technique with such capability is called Melt Electro Writing (MEW), and in practice, it refers to the basic working principle on which bio-printers are based. This paper aims to examine how these two techniques can be combined affordably. Comparatively, it presents output production processes, design components, parameters, and materials used in output production. It discusses the limitations and advantages of such a hybrid platform, specifically from the perspective of engineering design and its biomedical applications.
Li Y., Wang P., Zhai Y., Lv J., Sun Y.
Nanocrystalline FeCoNi medium‐entropy alloys (MEAs), characterized by their unique internal microstructure and substantial industrial application potential, often exhibit superior performance compared to conventional alloys and high‐entropy alloys. Herein, nanocrystalline FeCoNi MEAs are fabricated using an alternating current pulse electrodeposition method. The microstructure, crystallographic characteristics, and mechanical properties of the electrodeposited layers are systematically investigated. A MEA foil with a nanoscale grain thickness of 45 μm is successfully prepared. Furthermore, the foil is subjected to microbulging tests using a gas‐pressure microforming setup. The morphology and stress distribution of the deformed alloy are analyzed in detail.
Sadaghian H., Khalilzadehtabrizi S., Khodadoost S., Yeon J.H.
Abstract
Background
A myriad of materials, ranging from soft sensors to bone substitutes, undergo torsional loading throughout their operational lifespan. Many of these materials are produced using additive manufacturing (AM) technology due to its broad applicability. Understanding the torsional behavior of these AM components is crucial prior to their utilization. However, research on the torsional behavior of solid additively-manufactured resin polymers remains very limited.
Objective
To address the gap in understanding the torsional behavior of additively-manufactured resin polymers, this study aimed to investigate the effect of varying gage lengths and UV post-curing durations on the torsional capacity, shear modulus, and energy absorption characteristics of these materials.
Methods
Torsion specimens were fabricated using vat photopolymerization (VPP) with AnyCubic UV Tough Resin. The specimens were prepared with different gage lengths (20, 40, 60, and 80 mm) and were subjected to five UV post-curing durations (0, 15, 30, 60, 90, and 120 min). Monotonic torsion was applied to the specimens until failure at a rate of 0.1 revolutions per minute.
Results
The tests revealed ductile failure patterns across all specimens. Longer post-curing times were found to correlate with increased torsional capacities and shear moduli. However, conclusions regarding energy absorption per unit volume remained inconclusive. The results showed that UV exposure had a significantly greater impact on the mechanical properties of the specimens compared to the gage length. Additionally, a normalized trilinear model was proposed to characterize the behavior of additively-manufactured resin polymers under monotonic torsion, which facilitates numerical simulation of material responses in finite element software.
Tashkinov M., Pirogova Y., Kononov E., Shalimov A., Silberschmidt V.V.
Generative adversarial neural networks with a variational autoencoder (VAE-GANs) are actively used in the field of materials design. The synthesis of random structures with nonrepeated geometry and predetermined mechanical properties is important for solving various practical problems. Geometric parameters of such artificially generated random structures can vary within certain limits compared to the training dataset, causing unpredicted fluctuations in their resulting mechanical response. This study investigates the statistical variability of mechanical and morphological characteristics of random 3D models reconstructed from 2D images using a VAE-GAN neural network. A combined multitool method employing different mathematical and statistical instruments for comparison of the reconstructed models with their corresponding originals is proposed. It includes the analysis of statistical distributions of elastic properties, morphometric parameters, and stress values. The neural network was trained on two datasets, containing models created based on Gaussian random fields. Statistical fluctuations of the mechanical and morphological parameters of the reconstructed models are analyzed. The deviation of the effective elastic modulus of the reconstructed models from that of the original ones was less than 5.7% on average. The difference between the median values of ligament thickness and distance between ligaments ranged from 3.6 to 6.5% and 2.6 to 5.2%, respectively. The median value of the surface area of the reconstructed geometries was 4.6–8.1% higher compared to the original models. It is thus shown that mechanical properties of the NN-generated structures retain the statistical variability of the corresponding originals, while the variability of the morphology is highly affected by the training set and does not depend on the configuration of the input 2D image.
Elenskaya N., Vindokurov I., Sadyrin E., Nikolaev A., Tashkinov M.
Bone transplantation ranks second worldwide among tissue prosthesis surgeries. Currently, one of the most promising approaches is regenerative medicine, which involves tissue engineering based on polymer scaffolds with biodegradable properties. Once implanted, scaffolds interact directly with the surrounding tissues and in a fairly aggressive environment, which causes biodegradation of the scaffold material. The aim of this work is to experimentally investigate the changes in the effective mechanical properties of polylactide scaffolds manufactured using additive technologies. The mechanism and the rate of the degradation process depend on the chosen material, contact area, microstructural features, and overall architecture of sample. To assess the influence of each of these factors, solid samples with different dimensions and layers orientation as well as prototypes of functionally graded scaffolds were studied. The research methodology includes the assessment of changes in the mechanical properties of the samples, as well as their structural characteristics. Changes in the mechanical properties were measured in compression tests. Microcomputed tomography (micro-CT) studies were conducted to evaluate changes in the microstructure of scaffold prototypes. Changes caused by surface erosion and their impact on degradation were assessed using morphometric analysis. Nonlinear changes in mechanical properties were observed for both solid samples and lattice graded scaffold prototypes depending on the duration of immersion in NaCl solution and exposure to different temperatures. At the temperature of 37 °C, the decrease in the elastic modulus of solid specimens was no more than 16%, while for the lattice scaffolds, it was only 4%. For expedited degradation during a higher temperature of 45 °C, these ratios were 47% and 16%, respectively. The decrease in compressive strength was no more than 32% for solid specimens and 17% for scaffolds. The results of this study may be useful for the development of optimal scaffolds considering the impact of the degradation process on their structural integrity.
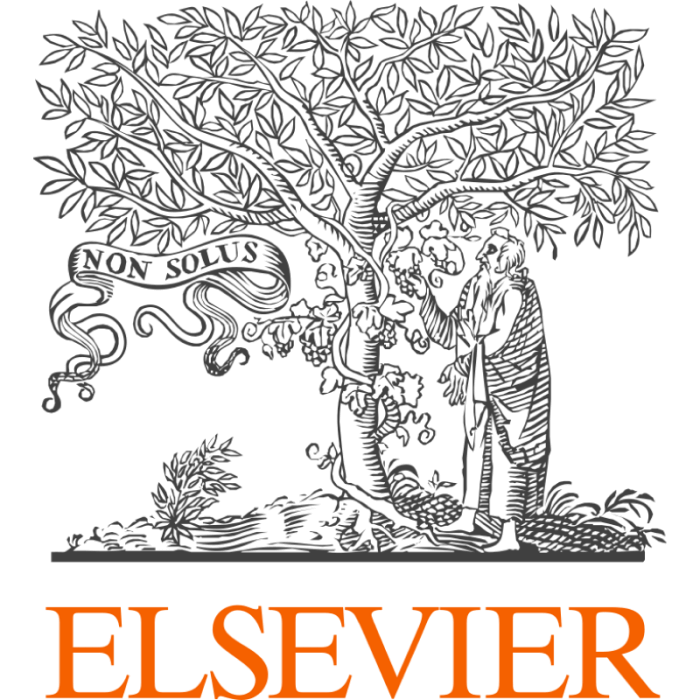
Mohammad A.H., Al-Waily M., Njim E.K., Jweeg M.J., Hameed A.A.
The Artificial Intervertebral Disc (IVD) is considered one of the modern medical developments aimed at treating some problems and diseases associated with the spine. The artificial intervertebral disc restores or improves the spine's function. It is also considered an emergency surgical option to help relieve pain and reduce the need for traditional spinal fixation operations. PLA is an easy-to-print polymer capable of achieving biocompatibility, making it suitable for medical and biomedical applications. This study studied porous functionally graded materials by choosing (PLA +) and manufacturing them with a three-dimensional printer with FDM technology to design artificial intervertebral discs for humans. For the reason that the artificial intervertebral disc in the L4-L5 segment is greatly affected by the tooth of overweight people, the intervertebral disc was discussed in terms of compressive stresses of different forces 2 KN, 4.75 KN, max load 80 KN experimentally, and 31 cases were studied with a porous gradient with the help of ANSYS22 R2 with the same forces in one case and another with the addition of the moment effect, 7.5 N. m with the same forces and the last case only moment. The compression test results showed the possibility of using porous compositions to reduce the change of the surface area of the disk artificial vertebra if it is subjected to high or medium loads. In the best sample model with a porous gradient of 8 layers, the first and last layers are sold, while the inner layers are porous with a porosity of 0.1. This is very important for the development of effective artificial intervertebral discs capable of maintaining the permanence of their work and reducing friction in the future by injecting them with a non-toxic medical gelatin substance and other medical specifications inside the pores and, thus, behavior similar to a human disc and at the same time a solution to back pain problems and with less guarantee than other methods manufactured for the same artificial intervertebral disc.
Vindokurov I., Tashkinov M., Silberschmidt V.V.
Materials for additive manufacturing (AM), such as PLA and PEEK, are often used in biomedical applications, which involve interaction with liquid media. Consequently, the degradation process is a part of the service life of such polymers that can alter their mechanical response due to gradual changes in materials’ properties. Studying the behaviour of polymers in such environments is thus important for the prediction of the mechanical performance of biomedical devices. This paper examines the process of accelerated degradation of AM PLA and PEEK samples in saline solution and distilled water at elevated temperatures. An analysis of changes in mechanical properties, such as tensile strength and density, of PLA and PEEK with the immersion time was performed. The influence of heat treatment on the degradation process was investigated. It was found that the degradation rate of PLA in distilled water was higher than in NaCl. The trends in density changes measured with hydrostatic weighing correspond to those in the strength properties of the studied samples.
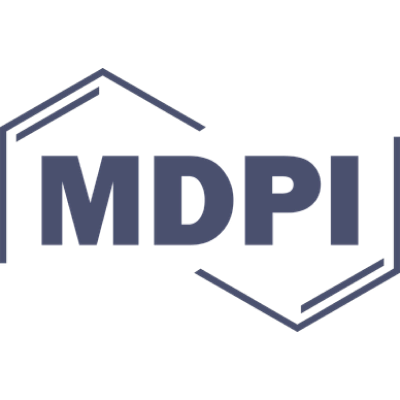
Alsaeed S.S., Abouelregal A.E., Elzayady M.E.
Poro-thermoelasticity models are crucial for analyzing porous materials in geotechnical engineering, such as how soil and rock respond to thermal and mechanical loads, fluid flow, and heat transmission. This study introduces a fractional dual-phase lag (DPL) porous thermoelasticity model using the Atangana-Baleanu fractional derivative to analyze thermoelastic responses in a material with unlimited porosity containing a spherical cavity under a pulsed magnetic field. The governing equations were solved using Laplace transforms, and numerical solutions were obtained by inverting the transforms. Graphical representations of deformation, temperature variation, and thermal stresses were generated for analysis. The results reveal significant insights into the behavior of porous materials like concrete and masonry under thermal and mechanical stress, aiding the development of more robust and flexible structures. For example, the proposed model predicts a 20 % reduction in the amount of thermal stress compared to conventional models, highlighting the influence of phase lag and fractional derivatives in accurately simulating realistic conditions.
Abouelregal A.E., Marin M., Askar S.S., Foul A.
Effect of temperature fluctuations on the thermo-mechanical properties of engineering materials can be critical in many engineering applications. Moreover, electromagnetic fields also affect the stresses and their distribution in addition to thermo-elastic stresses in some engineering materials, leading to a complex coupling between different energy domains. The proposed model enhances its ability to describe long-term interactions and memory effects by incorporating a non-singular kernel and non-local behavior. This suggestion is important because traditional thermoelasticity models often ignore non-local effects. Thermoelastic interactions in a thin, long, hollow tube immersed in a uniform electromagnetic field are considered. The Laplace transform method was applied to solve the governing equations in the transformed field, and the Dubner and Abate technique was applied to calculate the numerical results for the system fields. The results presented in the graphs were discussed, analyzed, and compared with the results of the corresponding traditional and generalized thermoelastic models, and the effect of operating factors and fractional order was studied. Changing the fractional derivative order improves memory and heredity. This slows changes in electric and magnetic fields and emphasizes dispersion.
Nothing found, try to update filter.
Fujita A., Goto K., Ueda A., Kuroda Y., Kawai T., Okuzu Y., Okuno Y., Matsuda S.
The purpose of this study was to reconstruct three-dimensional (3D) computed tomography (CT) images from single anteroposterior (AP) postoperative total hip arthroplasty (THA) X-ray images using a deep learning algorithm known as generative adversarial networks (GANs) and to validate the accuracy of cup angle measurement on GAN-generated CT.
Yuan X., Zhu W., Yang Z., He N., Chen F., Han X., Zhou K.
AbstractThe repair and functional reconstruction of bone defects resulting from severe trauma, surgical resection, degenerative disease, and congenital malformation pose significant clinical challenges. Bone tissue engineering (BTE) holds immense potential in treating these severe bone defects, without incurring prevalent complications associated with conventional autologous or allogeneic bone grafts. Three‐dimensional (3D) printing technology enables control over architectural structures at multiple length scales and has been extensively employed to process biomimetic scaffolds for BTE. In contrast to inert and functional bone grafts, next‐generation smart scaffolds possess remarkable ability to mimic the dynamic nature of native extracellular matrix (ECM), thereby facilitating bone repair and regeneration. Additionally, they can generate tailored and controllable therapeutic effects, such as antibacterial or antitumor properties, in response to exogenous and/or endogenous stimuli. This review provides a comprehensive assessment of the progress of 3D‐printed smart scaffolds for BTE applications. It begins with an introduction to bone physiology, followed by an overview of 3D printing technologies utilized for smart scaffolds. Notable advances in various stimuli‐responsive strategies, therapeutic efficacy, and applications of 3D‐printed smart scaffolds are discussed. Finally, the review highlights the existing challenges in the development and clinical implementation of smart scaffolds, as well as emerging technologies in this field.This article is protected by copyright. All rights reserved
Generale A.P., Robertson A.E., Kelly C., Kalidindi S.R.
Inverse Microstructure Design problems are ubiquitous in materials science; for example, property-driven microstructure design requires the inversion of a structure–property linkage. However, prior frameworks have struggled to address this problem's unique combination of challenges: the high dimensionality and stochasticity of microstructures, under sampled initial datasets, and ill-conditioning of the inversion. In this work, we propose a computational framework for Inverse Microstructure Design problems using a Bayesian methodology. We construct this framework from three modular components, enabling flexible extension and re-use. First, we define a low-dimensional, informative microstructure prior by integrating domain knowledge (i.e., statistical continuum mechanics) into a distributional learning scheme. This scheme includes multiple latent representations which address the challenges inherent to representing microstructures. Second, we define a property-specific likelihood using a multi-output Gaussian process regression surrogate model. Finally, we efficiently learn the conditional posterior density for a given target property, and generate samples using deep variational inference. We demonstrate our proposed method for solving stochastic microstructure design problems by identifying woven ceramic matrix composites matching target anisotropic thermal conductivities. Through this example, we analyze the integral role of each component in the inversion framework.
Pirogova Y., Tashkinov M., Vindokurov I., Silberschmidt V.V.
This paper studies the effect of different combinations of morphological parameters of porous closed-cell materials on their elastic properties and mechanical behaviour. Three-dimensional representative volumes of porous media with different polyhedral void shapes are investigated, considering variation of statistical realisations of morphological features, such as shape, size and distribution of pores. Description of morphology of each investigated representative volume is formalized using second- and fourth-order correlation functions. The effective properties of representative volumes are calculated with finite-element analysis. Additionally, samples of the studied models were additively manufactured with polystyrene, using fused filament fabrication (FFF/FDM) 3D-printing technique, and subjected to compression. Experimental results for elastic mechanical properties and distributions of strain fields on the surface of the samples, obtained with micro-DIC (digital image correlation), are compared with results of numerical finite-element computations. This is accompanied by analysis of internal-stress distributions to assess the mechanical state of the structures. Patterns and trends observed in mechanical responses of porous materials depending on their different morphological parameters are outlined and discussed.
Progress and Opportunities for Machine Learning in Materials and Processes of Additive Manufacturing
Ng W.L., Goh G.L., Goh G.D., Sheuan J.T., Yeong W.Y.
AbstractIn recent years, there has been a widespread adoption of machine learning (ML) technologies to unravel intricate relationships among diverse parameters in various additive manufacturing (AM) techniques. These ML models excel at recognizing complex patterns from extensive, well‐curated datasets, thereby unveiling latent knowledge crucial for informed decision‐making during the AM process. The collaborative synergy between ML and AM holds the potential to revolutionize the design and production of AM‐printed parts. By leveraging the copious data generated in AM processes, ML algorithms can significantly enhance design optimization. This is achieved by employing forward problem analysis in tandem with iterative optimization techniques or generative artificial intelligence tools. The approach involves reverse‐engineering from desired outcomes to yield valuable insights, ultimately streamlining the AM design process. This review paper delves into the challenges and opportunities emerging at the intersection of these two dynamic fields. It provides a comprehensive analysis of the publication landscape for ML‐related research in the field of AM, explores common ML applications in AM research (such as quality control, process optimization, design optimization, microstructure analysis, and material formulation) and concludes by presenting an outlook that underscores the utilization of advanced ML models, the development of emerging sensors, and ML applications in emerging AM‐related fields. Notably, ML has garnered increased attention in AM due to its superior performance across various AM‐related applications. We envision that the integration of ML into AM processes will significantly enhance 3D printing capabilities across diverse AM‐related research areas.
This article is protected by copyright. All rights reserved
Wu C., Wan B., Entezari A., Fang J., Xu Y., Li Q.
While ceramic additive manufacturing (AM) technologies have shown great promise to create functional scaffolds with tailored biomechanical properties, the true potential of these advanced techniques has not been fully exploited yet due to lack of practical optimisation design approaches. To address this challenge, a machine learning (ML)-based design approach is proposed herein where ceramic 3D printing techniques are combined to fabricate functionally graded scaffolds composed of Triply Periodic Minimal Surfaces (TPMS), aiming to fulfil the anticipated biomechanical requirements of the target bone regeneration outcomes. The proposed ML based design strategy couples a Bayesian optimisation (BO) algorithm to enable time-dependent mechano-biological optimisation of the 3D printed ceramic scaffolds at a reasonably low computational cost. For a representative example relating to bone scaffolding in a segmental defect of sheep tibia, the simulated results demonstrate that the optimised functionally graded scaffolds significantly enhance bone ingrowth outcomes. Furthermore, a Lithography-based Ceramic Manufacturing (LCM) technique is employed to fabricate the optimised scaffolds based on the proposed ML-based design framework, followed by micro-CT analyses of the additively manufactured ceramic scaffolds to assess their geometric qualities. This study is expected to gain new insights into mechanical sciences on design for varying material conditions and provide an effective design tool for ceramic additive manufacturing.
Lyu X., Ren X.
AbstractMicrostructure reconstruction serves as a crucial foundation for establishing process–structure–property (PSP) relationship in material design. Confronting the limitations of variational autoencoder and generative adversarial network within generative models, this study adopted the denoising diffusion probabilistic model (DDPM) to learn the probability distribution of high-dimensional raw data and successfully reconstructed the microstructures of various composite materials, such as inclusion materials, spinodal decomposition materials, chessboard materials, fractal noise materials, and so on. The quality of generated microstructure was evaluated using quantitative measures like spatial correlation functions and Fourier descriptor. On this basis, this study also achieved the regulation of microstructure randomness and the generation of gradient materials through continuous interpolation in latent space using denoising diffusion implicit model (DDIM). Furthermore, the two-dimensional microstructure reconstruction was extended to three-dimensional framework and integrated permeability as a feature encoding embedding. This enables the conditional generation of three-dimensional microstructures for random porous materials within a defined permeability range. The permeabilities of these generated microstructures were further validated through the application of the lattice Boltzmann method. The above methods provide new ideas and references for material reverse design.
Molnár S., Tamás L.
AbstractVariational autoencoders (VAEs) play an important role in high-dimensional data generation based on their ability to fuse the stochastic data representation with the power of recent deep learning techniques. The main advantages of these types of generators lie in their ability to encode the information with the possibility to decode and generalize new samples. This capability was heavily explored for 2D image processing; however, only limited research focuses on VAEs for 3D data processing. In this article, we provide a thorough review of the latest achievements in 3D data processing using VAEs. These 3D data types are mostly point clouds, meshes, and voxel grids, which are the focus of a wide range of applications, especially in robotics. First, we shortly present the basic autoencoder with the extensions towards the VAE with further subcategories relevant to discrete point cloud processing. Then, the 3D data specific VAEs are presented according to how they operate on spatial data. Finally, a few comprehensive table summarizing the methods, codes, and datasets as well as a citation map is presented for a better understanding of the VAEs applied to 3D data. The structure of the analyzed papers follows a taxonomy, which differentiates the algorithms according to their primary data types and application domains.
Yu M., Jung T., Yun D., Hwang C., Park S., Kwon S., Jung K.
Generative Adversarial Networks (GANs) for 3D volume generation and reconstruction, such as shape generation, visualization, automated design, real-time simulation, and research applications, are receiving increased amounts of attention in various fields. However, challenges such as limited training data, high computational costs, and mode collapse issues persist. We propose combining a Variational Autoencoder (VAE) and a GAN to uncover enhanced 3D structures and introduce a stable and scalable progressive growth approach for generating and reconstructing intricate voxel-based 3D shapes. The cascade-structured network involves a generator and discriminator, starting with small voxel sizes and incrementally adding layers, while subsequently supervising the discriminator with ground-truth labels in each newly added layer to model a broader voxel space. Our method enhances the convergence speed and improves the quality of the generated 3D models through stable growth, thereby facilitating an accurate representation of intricate voxel-level details. Through comparative experiments with existing methods, we demonstrate the effectiveness of our approach in evaluating voxel quality, variations, and diversity. The generated models exhibit improved accuracy in 3D evaluation metrics and visual quality, making them valuable across various fields, including virtual reality, the metaverse, and gaming.
Chiang Y., Tseng B., Wang J., Chen Y., Tung C., Yu C., Chen P., Chen C.
Biomaterials possess extraordinary properties due to intricate structures on the microscale. Learning from these microstructures is critical for the design of high-performance materials with multiple functions. However, explicit modeling of the microstructures is not always feasible. This study developed a deep generative network with a self-attention mechanism to generate three-dimensional (3D) bioinspired microstructures. The robustness of the model was first checked by generating a series of gyroids, a mathematically well-defined microstructure, which showed excellent consistency with the desired structures. The model was then applied to the microstructure of the elk antlers, which are complex and cannot be directly expressed mathematically. The results showed that the model also performs well in complex, ill-defined biological materials. The model learned the inherent patterns, generating different structures with similar geometric features. This study demonstrates the potential of using Transformer-based deep generative models that can be used to generate novel 3D microstructures from limited high-resolution X-ray micro-computed tomography data.
Elenskaya N., Tashkinov M., Vindokurov I., Pirogova Y., Silberschmidt V.V.
Applications of additive manufacturing (AM) in tissue engineering develop rapidly. AM offers layer-by-layer creation of complex objects, developed to restore functionality of, or replace, damaged tissues. Porous 3D-printed functional gradient structures are of particular interest: their special architecture makes it possible to simulate the heterogeneity of the replaced tissue and, by continuously changing the mechanical properties, to avoid the concentration of stresses that can be caused by abrupt geometric changes. Such structures also allow combinations of different types of unit cells and a smooth transition between them, making design of personalised scaffolds with optimal parameters for the replacement of damaged host tissue at the interface between tissues possible. This paper presents the results of development of scaffold structures with gradients of porosity and multi-morphology using unit cells based on triply periodic minimal surfaces (TPMS). The mechanical behaviour of additively manufactured scaffold prototypes made of polylactide acid (PLA) was studied under compressive loading. Strain fields on their surface were captured using the Vic-3d Micro-DIC digital image correlation system and compared with those obtained with detailed numerical simulations, employing elastic-plastic properties of PLA, obtained in experiments. The effect of gradient parameters and unit-cell morphology on the stress distribution in scaffolds was analysed. A smooth gradient transition between cells with different morphologies was found to reduce the probability of structural failure under intense compressive loading. A good agreement between numerical results and experimental data was achieved, which justifies application of the developed approach to design of personalised bone scaffolds.
Brown N.K., Garland A.P., Fadel G.M., Li G.
Mechanical metamaterials are artificial materials with unique global properties due to the structural geometry and material composition of their unit cell. Typically, mechanical metamaterial unit cells are designed such that, when tessellated, they exhibit unique mechanical properties such as zero or negative Poisson's ratio and negative stiffness. Beyond these applications, mechanical metamaterials can be used to achieve tailorable nonlinear deformation responses. Computational methods such as gradient-based topology optimization (TO) and size/shape optimization (SSO) can be implemented to design these metamaterials. However, both methods can lead to suboptimal solutions or a lack of generalizability. Therefore, this research used deep reinforcement learning (DRL), a subset of deep machine learning that teaches an agent to complete tasks through interactive experiences, to design mechanical metamaterials with specific nonlinear deformation responses in compression or tension. The agent learned to design the unit cells by sequentially adding material to a discrete design domain and being rewarded for achieving the desired deformation response. After training, the agent successfully designed unit cells to exhibit desired deformation responses not experienced during training. This work shows the potential of DRL as a high-level design tool for a wide array of engineering applications.
Zheng X., Zhang X., Chen T., Watanabe I.
AbstractMechanical metamaterials are meticulously designed structures with exceptional mechanical properties determined by their microstructures and constituent materials. Tailoring their material and geometric distribution unlocks the potential to achieve unprecedented bulk properties and functions. However, current mechanical metamaterial design considerably relies on experienced designers' inspiration through trial and error, while investigating their mechanical properties and responses entails time‐consuming mechanical testing or computationally expensive simulations. Nevertheless, recent advancements in deep learning have revolutionized the design process of mechanical metamaterials, enabling property prediction and geometry generation without prior knowledge. Furthermore, deep generative models can transform conventional forward design into inverse design. Many recent studies on the implementation of deep learning in mechanical metamaterials are highly specialized, and their pros and cons may not be immediately evident. This critical review provides a comprehensive overview of the capabilities of deep learning in property prediction, geometry generation, and inverse design of mechanical metamaterials. Additionally, this review highlights the potential of leveraging deep learning to create universally applicable datasets, intelligently designed metamaterials, and material intelligence. This article is expected to be valuable not only to researchers working on mechanical metamaterials but also those in the field of materials informatics.
Motiee E., Karbasi S., Bidram E., Sheikholeslam M.
Mechanical properties appropriate to native tissues, as an essential component in bone tissue engineering scaffolds, plays a significant role in tissue formation. In the current study, Poly-3 hydroxybutyrate-chitosan (PC) scaffolds reinforced with graphene oxide (GO) were made by the electrospinning method. The addition of GO led to a decrease in fibers diameter, an increase in thermal capacity and an improvement in the surface hydrophilicity of nanocomposite scaffolds. A significant increase in the mechanical properties of PC/GO (PCG) nanocomposite scaffolds was achieved due to the inherent strength of GO as well as its uniform dispersion throughout the polymeric matrix owing to hydrogen bonding and polar interactions. Also, lower biological degradation of the scaffolds (~30% in 100 days) due to the presence of GO provides essential mechanical support for bone regeneration. In addition, the bioactivity results showed that GO reinforcement significantly increases the biomineralization on the surface of the scaffolds. Evaluating cell adhesion and proliferation, as well as ALP activity of MG-63 cells on PC and PCG scaffolds indicated the positive effect of GO on scaffolds' biocompatibility. Overall, the improvement of physicochemical, mechanical, and biological properties of GO-reinforced scaffolds shows the potential of PCG nanocomposite scaffolds for bone tissue engineering.
Total publications
6
Total citations
33
Citations per publication
5.5
Average publications per year
2
Average coauthors
3
Publications years
2022-2024 (3 years)
h-index
4
i10-index
1
m-index
1.33
o-index
8
g-index
5
w-index
1
Metrics description
h-index
A scientist has an h-index if h of his N publications are cited at least h times each, while the remaining (N - h) publications are cited no more than h times each.
i10-index
The number of the author's publications that received at least 10 links each.
m-index
The researcher's m-index is numerically equal to the ratio of his h-index to the number of years that have passed since the first publication.
o-index
The geometric mean of the h-index and the number of citations of the most cited article of the scientist.
g-index
For a given set of articles, sorted in descending order of the number of citations that these articles received, the g-index is the largest number such that the g most cited articles received (in total) at least g2 citations.
w-index
If w articles of a researcher have at least 10w citations each and other publications are less than 10(w+1) citations, then the researcher's w-index is equal to w.
Top-100
Fields of science
1
2
|
|
Polymers and Plastics
|
Polymers and Plastics, 2, 33.33%
Polymers and Plastics
2 publications, 33.33%
|
Mechanics of Materials
|
Mechanics of Materials, 2, 33.33%
Mechanics of Materials
2 publications, 33.33%
|
General Chemistry
|
General Chemistry, 1, 16.67%
General Chemistry
1 publication, 16.67%
|
Organic Chemistry
|
Organic Chemistry, 1, 16.67%
Organic Chemistry
1 publication, 16.67%
|
Condensed Matter Physics
|
Condensed Matter Physics, 1, 16.67%
Condensed Matter Physics
1 publication, 16.67%
|
General Materials Science
|
General Materials Science, 1, 16.67%
General Materials Science
1 publication, 16.67%
|
Mechanical Engineering
|
Mechanical Engineering, 1, 16.67%
Mechanical Engineering
1 publication, 16.67%
|
Biomaterials
|
Biomaterials, 1, 16.67%
Biomaterials
1 publication, 16.67%
|
General Engineering
|
General Engineering, 1, 16.67%
General Engineering
1 publication, 16.67%
|
Energy Engineering and Power Technology
|
Energy Engineering and Power Technology, 1, 16.67%
Energy Engineering and Power Technology
1 publication, 16.67%
|
Biomedical Engineering
|
Biomedical Engineering, 1, 16.67%
Biomedical Engineering
1 publication, 16.67%
|
Applied Mathematics
|
Applied Mathematics, 1, 16.67%
Applied Mathematics
1 publication, 16.67%
|
Modeling and Simulation
|
Modeling and Simulation, 1, 16.67%
Modeling and Simulation
1 publication, 16.67%
|
1
2
|
Journals
1
|
|
International Journal of Solids and Structures
1 publication, 16.67%
|
|
Mathematics
1 publication, 16.67%
|
|
Polymers
1 publication, 16.67%
|
|
Journal of the Mechanical Behavior of Biomedical Materials
1 publication, 16.67%
|
|
Polymer Testing
1 publication, 16.67%
|
|
Procedia Structural Integrity
1 publication, 16.67%
|
|
1
|
Citing journals
1
2
3
4
|
|
Polymers
4 citations, 11.76%
|
|
International Journal of Advanced Manufacturing Technology
4 citations, 11.76%
|
|
Medical Engineering and Physics
3 citations, 8.82%
|
|
Micromachines
2 citations, 5.88%
|
|
Computers in Biology and Medicine
2 citations, 5.88%
|
|
Polymer Testing
2 citations, 5.88%
|
|
Journal of Vibrational Engineering and Technologies
1 citation, 2.94%
|
|
Case Studies in Thermal Engineering
1 citation, 2.94%
|
|
Biotribology
1 citation, 2.94%
|
|
Experimental Mechanics
1 citation, 2.94%
|
|
Journal of Tissue Engineering
1 citation, 2.94%
|
|
Mathematics
1 citation, 2.94%
|
|
Composites Part B: Engineering
1 citation, 2.94%
|
|
Results in Engineering
1 citation, 2.94%
|
|
Progress in Additive Manufacturing
1 citation, 2.94%
|
|
Materials Today Communications
1 citation, 2.94%
|
|
Additive Manufacturing
1 citation, 2.94%
|
|
Frontiers in Bioengineering and Biotechnology
1 citation, 2.94%
|
|
Lecture Notes in Networks and Systems
1 citation, 2.94%
|
|
Journal of Materials Research and Technology
1 citation, 2.94%
|
|
Advanced Engineering Materials
1 citation, 2.94%
|
|
Multiscale and Multidisciplinary Modeling Experiments and Design
1 citation, 2.94%
|
|
Engineering Research Express
1 citation, 2.94%
|
|
1
2
3
4
|
Publishers
1
2
3
4
|
|
Elsevier
4 publications, 66.67%
|
|
MDPI
2 publications, 33.33%
|
|
1
2
3
4
|
Organizations from articles
1
2
3
4
|
|
Perm National Research Polytechnic University
4 publications, 66.67%
|
|
Loughborough University
4 publications, 66.67%
|
|
Organization not defined
|
Organization not defined, 2, 33.33%
Organization not defined
2 publications, 33.33%
|
1
2
3
4
|
Countries from articles
1
2
3
4
|
|
Russia
|
Russia, 4, 66.67%
Russia
4 publications, 66.67%
|
United Kingdom
|
United Kingdom, 4, 66.67%
United Kingdom
4 publications, 66.67%
|
Country not defined
|
Country not defined, 2, 33.33%
Country not defined
2 publications, 33.33%
|
1
2
3
4
|
Citing organizations
1
2
3
4
5
6
7
8
9
|
|
Organization not defined
|
Organization not defined, 9, 27.27%
Organization not defined
9 citations, 27.27%
|
Perm National Research Polytechnic University
7 citations, 21.21%
|
|
Loughborough University
6 citations, 18.18%
|
|
Polytechnic University of Turin
2 citations, 6.06%
|
|
Mansoura University
2 citations, 6.06%
|
|
Don State Technical University
1 citation, 3.03%
|
|
Al Jouf University
1 citation, 3.03%
|
|
University of Tabriz
1 citation, 3.03%
|
|
University of Baghdad
1 citation, 3.03%
|
|
University of Kufa
1 citation, 3.03%
|
|
Sichuan University
1 citation, 3.03%
|
|
Jilin University
1 citation, 3.03%
|
|
Istinye University
1 citation, 3.03%
|
|
Lulea University of Technology
1 citation, 3.03%
|
|
Aalto University
1 citation, 3.03%
|
|
Capital Medical University
1 citation, 3.03%
|
|
Shanxi Medical University
1 citation, 3.03%
|
|
Chengdu University
1 citation, 3.03%
|
|
China Medical University (Liaoning)
1 citation, 3.03%
|
|
Air Force Medical University
1 citation, 3.03%
|
|
Qingdao University
1 citation, 3.03%
|
|
Guangxi Medical University
1 citation, 3.03%
|
|
Universidad Autónoma de Baja California
1 citation, 3.03%
|
|
Universidad de Sonora
1 citation, 3.03%
|
|
University of Minho
1 citation, 3.03%
|
|
University of Aveiro
1 citation, 3.03%
|
|
1
2
3
4
5
6
7
8
9
|
Citing countries
2
4
6
8
10
|
|
Country not defined
|
Country not defined, 10, 30.3%
Country not defined
10 citations, 30.3%
|
Russia
|
Russia, 7, 21.21%
Russia
7 citations, 21.21%
|
United Kingdom
|
United Kingdom, 6, 18.18%
United Kingdom
6 citations, 18.18%
|
China
|
China, 3, 9.09%
China
3 citations, 9.09%
|
Egypt
|
Egypt, 2, 6.06%
Egypt
2 citations, 6.06%
|
Italy
|
Italy, 2, 6.06%
Italy
2 citations, 6.06%
|
Saudi Arabia
|
Saudi Arabia, 2, 6.06%
Saudi Arabia
2 citations, 6.06%
|
USA
|
USA, 1, 3.03%
USA
1 citation, 3.03%
|
Portugal
|
Portugal, 1, 3.03%
Portugal
1 citation, 3.03%
|
Iraq
|
Iraq, 1, 3.03%
Iraq
1 citation, 3.03%
|
Iran
|
Iran, 1, 3.03%
Iran
1 citation, 3.03%
|
Mexico
|
Mexico, 1, 3.03%
Mexico
1 citation, 3.03%
|
Romania
|
Romania, 1, 3.03%
Romania
1 citation, 3.03%
|
Turkey
|
Turkey, 1, 3.03%
Turkey
1 citation, 3.03%
|
Finland
|
Finland, 1, 3.03%
Finland
1 citation, 3.03%
|
Sweden
|
Sweden, 1, 3.03%
Sweden
1 citation, 3.03%
|
2
4
6
8
10
|
- We do not take into account publications without a DOI.
- Statistics recalculated daily.
This section displays the profiles of scientists registered on the platform. To display the full list, invite your colleagues to register.