Особая подготовка позволила «настроить» свойства сплавов даже после закалки
Ученые разработали формулу для производства высокопрочных сплавов с сохранением аморфного эффекта, когда материал обладает твердостью, но при этом лишен кристаллической решетки. Благодаря предложенному подходу форму и свойства материалов можно настраивать, сохраняя прочность. Это позволит дольше эксплуатировать сплавы в промышленности и использовать их вместо импортных материалов.
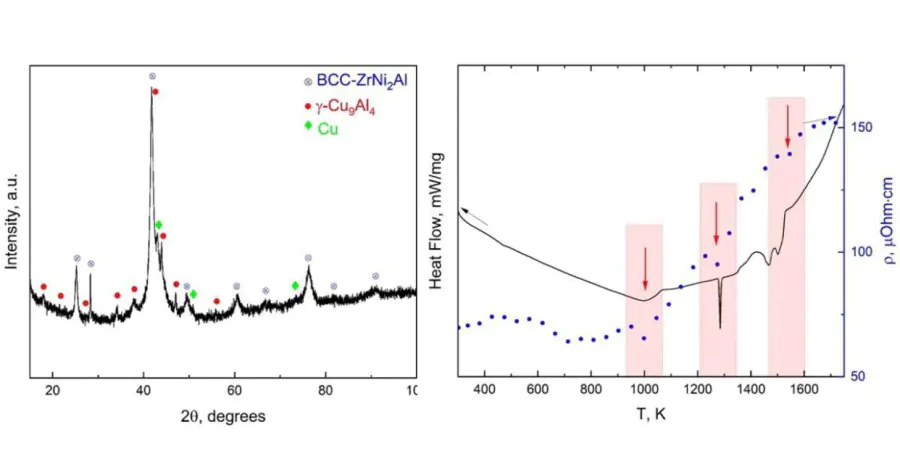
Сплавы металлов широко применяются в промышленности, в авиа- и машиностроении, а также в электронике. Для их изготовления обычно используют два популярных метода — кристаллизацию и порошковую металлургию. В первом случае металлы из жидкого состояния переводят в твердое и доводят до однородной консистенции за счет высокой температуры. А во втором сплавы формируются в результате спрессовывания смеси различных порошков, которые отправляются в специальную печь и проходят цикл высокотемпературной обработки. Далее получаемые материалы обычно закаливают, нагревая до высоких температур с последующим быстрым охлаждением. Однако многие металлы и сплавы с высокой твердостью после закаливания плохо режутся в процессе изготовления деталей. Также плохо поддаются обработке металлы с низкой твердостью. Например, сплавы на основе кобальта и редкоземельных металлов.
Ученые из Уральского государственного педагогического университета (Екатеринбург) впервые синтезировали эквиатомный, то есть содержащий компоненты в равных долях, сплав на основе алюминия, никеля, кобальта, меди и циркония. Эти металлы, концентрация каждого из которых составила 20%, широко используются в промышленности и придают разные конечные свойства сплаву. Так, алюминий, кобальт и цирконий повышают коррозионную стойкость, никель — твердость, медь — пластичность. Но главное их преимущество — образование аморфного состояния, при котором в сплаве отсутствует кристаллическая структура, характерная для обычных металлов. В таком состоянии сплавы приобретают лучшие механические свойства. Аморфные образцы сплава ученые получили в виде стержней методом вакуумного всасывания. Данный метод заключается в следующем: жидкий расплав под давлением втягивается в охлаждаемую цилиндрическую форму (медную изложницу), в результате чего затвердевает в виде стержня. Так как скорость охлаждения при таком втягивании расплава очень большая, кристаллическая структура не успевает сформироваться, и получается аморфный образец.
Ученые предварительно подготовили сплав в жидком состоянии к закалке, опираясь на данные о его свойствах (плотности, электрическом сопротивлении, магнитной восприимчивости). Процесс подготовки заключался в нагреве расплавов до 1370-1420°C, что существенно выше температуры плавления (1250°C). Это позволило сделать расплав более однородным. При быстрой закалке после такой подготовки в зависимости от концентрации компонентов формируется качественная аморфная фаза (без кристаллических включений) или высокотемпературные фазы — как правило соединения алюминия и меди, циркония и переходных металлов (кобальта и никеля), которые невозможно получить при низких скоростях охлаждения.
Физики также экспериментально исследовали плотность сплава, используя проникающее гамма-излучение. Таким образом авторы детально изучили особенности сплава в жидком состоянии и определили режимы, которые позволят подготовить его к быстрозакаленному состоянию. Эти данные позволят получать материалы с желаемыми свойствами. Например, предварительная подготовка сплава перед закалкой поможет образовать требуемые фазы, которые имеют высокие значения механических и коррозионных свойств.
«Полученный нами сплав можно использовать как материал для различных устройств, например, электромагнитных датчиков. Мы продолжаем изучать сплавы системы Al-Ni-Co-Cu-Zr, в том числе их механические и коррозионные свойства. Но уже сейчас можно сказать, что образованная структура сплава при быстрой закалке может обеспечить высокие показатели микротвердости, прочности и коррозионной стойкости. Большинство сплавов, имеющих похожие свойства, получают на основе хрома, железа и редкоземельных металлов. Эти компоненты существенно дороже тех, что использовали мы. В ближайшее время коллектив начнет исследовать коррозионные свойства сплавов предложенной композиции с различным соотношением компонентов. Это даст понимание, можно ли их применять в агрессивных средах, например в морской воде. Комплексное изучение сплавов позволит создавать собственные критически важные комплектующие, заменив импортные», — рассказывает руководитель проекта, поддержанного грантом РНФ, Борис Русанов, кандидат физико-математических наук, старший научный сотрудник УрГПУ.