Raad, Saad Al-Haidari
Lecturer, Associate member of the Australian Academy of Technological Sciences and Engineering
🥼
🥼
Saad can become your supervisor
If you would like to work under his/her guidance, please write a message or contact him/her on social media.
Authorization required.
Please confirm your email.
Thanks for signing up! Before getting started, could you verify your email address by clicking on the link we just emailed to you? If you didn't receive the email, we will gladly send you another.
🤝
🤝
Saad is looking for opportunities for scientific collaboration
If you would like to do joint research with him/her, write a message or contact him/her on social media.
Authorization required.
Please confirm your email.
Thanks for signing up! Before getting started, could you verify your email address by clicking on the link we just emailed to you? If you didn't receive the email, we will gladly send you another.
Publications
6
Citations
40
h-index
3
Research interests
Computational fluid dynamics (CFD)
Fluid flow
Fluid mechanics
Heat and mass transfer
Heat exchangers
Heat resistance
Heat sinks
Heat transfer enhancement
Mathematical and simulation modeling
Modelling and Simulations
Numerical simulation
Performance evaluation factor
Pressure drops
Solar energy
THERMAL ENGINEERING
Thermohydraulic flow
Nothing found, try to update filter.
Al‐Haidari S.R., Al‐Obaidi A.R.
ABSTRACTThis study explored the influence of geometric parameters on corrugated tube heat exchangers under turbulent flow conditions. Eighteen different configurations were evaluated using both numerical simulations and experimental methods. The simulations, ranging from Reynolds numbers of 4000 to 15,000, analyzed various tube diameters, shapes, and disturbances. Results demonstrated that dimpled tube configurations significantly enhanced heat transfer compared with smooth tubes. The best performance, a pressure drop efficiency of 1.41 at a Reynolds number of 4000, was achieved with 2‐mm dimples spaced 20 mm apart in an in‐line pattern. Validation of the numerical results against experimental data demonstrated a high level of accuracy. The maximum deviation for the Nusselt number was 12% in smooth tubes and 15% in dimpled tubes. The maximum deviation for the friction factor was 6.1% in smooth tubes and 8.3% in dimpled tubes. The numerical model accurately represented the full dimensions of a commercial heat exchanger. Grid independence tests were conducted using a three‐dimensional unstructured. To ensure accurate results, the study used a tetrahedral mesh and a Realizable k–ε turbulence model in its simulations. The findings revealed that corrugated tubes with various ring and dimple configurations dramatically enhanced heat transfer. Specifically, tubes with diameter rings, distance between rings, dimpled‐ring diameters, and distance between dimple rings achieved maximum enhancements of 45.5%, 35.009%, 67.95%, and 58.42%, respectively. Furthermore, dimpled tubes with different diameters and distances also outperformed smooth tubes, showing heat transfer increases of 42% and 38.8%. The optimized dimpled tube design offers a promising approach for improving heat exchanger performance while minimizing pressure drop. Future research can build upon these findings to further refine and optimize corrugated tube heat exchanger technology.
Al‐Haidari S.R., Al‐Obaidi A.R.
ABSTRACTCorrugated pipe is used in many engineering applications because of its high performance compared with smooth pipe. This research involved numerical simulations and experimental testing of a circular tube with a modified flow path to improve the heat transfer performance of heat exchangers. The focus was on enhancing mixing and creating vortex flows within the tube to increase heat exchange efficiency. The impact of seven design factors, including ring diameters (RD) and the pitch between ring pitches (RP), on thermal–hydraulic performance was investigated. Water is used as the working fluid and the flow regime ranges from 4000 to 15,000, indicating turbulent flow. A constant heat flux of 25,500 W/m2 is applied, and the water enters the system at a temperature of 298 K (25°C). The properties of water are assumed to remain constant throughout the flow with flow conditions, such as a steady state (the flow conditions do not change with time), incompressible flow (the density of the fluid remains constant), and no‐slip condition (the fluid velocity at the surface of any solid boundary is zero). Corrugated tubes consistently outperformed smooth tubes in heat transfer due to increased flow mixing and separation. Both increasing the Reynolds number and decreasing the design factors led to the formation of mixing and vortex patterns. In RD configurations, the Nusselt number saw an average improvement of approximately 45.6%, while the friction factor increased between 19% and 57%. RP configurations demonstrated a broader range of Nusselt number enhancements, reaching up to 35%, and friction factor increases ranging from 15% to 42%. Rings can significantly enhance the thermal–hydraulic performance of tubes. However, the best configuration depends on the specific application. The configuration with the highest performance, resulting in a 1.38 increase in performance evaluation factor, was obtained using an RD of 1 mm and an RP of 20 mm. The simulated and experimental data showed excellent agreement, with a maximum discrepancy of less than 11% for both smooth and dimpled tubes.
Al‐Haidari S.R., Al‐Obaidi A.R.
ABSTRACTIn the current work, the study examines the flow patterns and heat transfer capabilities of tubes with various spherical dimple configurations. A numerical analysis, supported by experimental validation on a reference model, was conducted on a circular tube with an alternating flow path. The primary goal was to enhance the thermal performance of circular tubes by inducing mixing and vortex flows. The impact of three design factors on thermal–hydraulic performance was investigated, dimple pipe diameter (DPD), dimple group number (DGN), and number of dimples (NODs). Dimpled tubes consistently outperformed smooth tubes in heat transfer due to increased flow mixing and separation. Both increasing the Reynolds number and decreasing the design factors led to the formation of mixing and vortex patterns. The performance evaluation factor (PEF) varied across different dimple configurations. For DPD, PEF ranged from 1.14 to 1.33; for DGN, it ranged from 1.15 to 1.28; for NOD, it ranged from 0.95 to 1.21, all within a Reynolds number range of 4000–15,000. At a Reynolds number of 6000, all three configurations of DPD, DGN, and NOD outperformed the smooth pipe in terms of the Nusselt number. For DPD, Nusselt number improvements ranged from 25.7% to 30.8%, and friction factors increased by 21% to 67%. DGN configurations exhibited a wider range of Nusselt number enhancement from 25% to 49.6%, and friction factor increase from 37% to 72%. NOD configurations also demonstrated consistent improvements, with Nusselt number increases ranging from 27.35% to 31% and friction factor increases from 42% to 74%. Spherical dimples can significantly enhance the thermal–hydraulic performance of tubes, so the best configuration depends on the specific application, and the highest performance, with a 1.33 increase in PEF, was achieved with a dimple diameter of 2 mm (DPD = 2 mm) and a dimple density of four dimples per unit area (NOD = 4).
Al‐Haidari S.R., Al‐Obaidi A.R.
AbstractEnhanced pipe surfaces offer greater heat transfer enhancement due to increased turbulence levels, leading to improved heat exchange performance. This study combines numerical simulations and experimental work to identify the best geometric design of enhanced tubes for thermal–hydraulic performance, flow structure, and pressure drop, and the simulations are validated with experimental data. Water is a working fluid with Reynolds numbers ranging from 4000 to 15,000, q = 25,500 W/m2, and an inlet temperature of 298 K with constant fluid property, steady state, and no‐slip condition. The three‐dimensional steady incompressible turbulent flow in the concavity dimpled shape‐enhanced tubes is numerically studied. This research found that pipes with a concave shape transfer heat most effectively. The overall heat transfer is significantly influenced by the shape of the dimples, their arrangement in rings, the size of these rings, and the number of rings. However, the number of cylindrical dimples does not seem to impact heat transfer much. The increase in heat transfer performance was by 9.8%–61% for dimple rings = 2ring performed best compared with a smooth pipe and by 8.21%–38.49% at the effect of ring numbers as grouping, also the dimple ring diameters by 5%–38% and by 7%–39% at dimple numbers. The performance evaluation factor (PEF) assesses overall performance by considering both the pressure drop penalty and improved heat transfer. The optimal configuration achieving the highest performance (PEF = 1.295) at a flow rate (Re) of 4000 involves a single dimple ring with a 2‐mm diameter, spaced 10‐mm apart, containing four dimples. Furthermore, discussing the different parameters of thermal and hydraulic performances to obtain the best thermal performance, and increasing the number and size of dimples gives a better guide for engineering to obtain better thermohydraulic performances for heat exchangers.
Al‐Haidari S.R., Al‐Obaidi A.R.
AbstractThis research work investigates how different dimple designs affect the flow field and thermal performance of three‐dimensional pipes. The study focuses on the effect of the number of improved dimples NOD (3, 4, and 5), different groups numbers DGNs (1, 2, and 3 groups), arranged around the pipe, and different distances between dimples (DBDs). Dimple geometry affects flow: Changing dimple parameters alters the velocity and pressure distribution within the pipe. Performance evaluation factor (PEF) varies with dimple configuration: The PEF, which balances heat transfer enhancement and pressure drop penalty, ranges from 1.187 to 1.23 for NOD and from 1.292 to 1.31 for DGN, and also from 1.26 to 1.302 for DBD. Reynolds number range, Re = 4000–15,000; turbulence model, standard k–ε model; numerical scheme, second‐order upwind scheme; test tube conditions, inlet temperature (Tin) = 25°C; pipe diameter D = 23 mm; thickness = 2 mm; heat flux q = 25,500 W/m²; and material (Cu). This research focuses on improving heat transfer efficiency in pipes using dimples. Dimple size and arrangement significantly impact flow dynamics and heat transfer. PEF is used to evaluate the overall performance considering both heat transfer improvement and pressure drop penalty. The study found a specific range for PEF under various conditions for different dimple configurations. The average enhancement in Nusselt number for model 2 was 15.16% compared with a smooth pipe and the heat transfer performance by 10.028%–28.963% at the effect of NOD, the DGN has slightly higher Nu values than smooth pipes, indicating improved heat transfer due to the dimples (around 7%–58% at Re 4000–15,000 and 9%–13% at Re 12,000), and at DBD (13.5%) at a Reynolds number of 12,000 and 4.6%–59% at Re 4000–15,000.
Nothing found, try to update filter.
Al‐Haidari S.R., Al‐Obaidi A.R.
ABSTRACTThis study explored the influence of geometric parameters on corrugated tube heat exchangers under turbulent flow conditions. Eighteen different configurations were evaluated using both numerical simulations and experimental methods. The simulations, ranging from Reynolds numbers of 4000 to 15,000, analyzed various tube diameters, shapes, and disturbances. Results demonstrated that dimpled tube configurations significantly enhanced heat transfer compared with smooth tubes. The best performance, a pressure drop efficiency of 1.41 at a Reynolds number of 4000, was achieved with 2‐mm dimples spaced 20 mm apart in an in‐line pattern. Validation of the numerical results against experimental data demonstrated a high level of accuracy. The maximum deviation for the Nusselt number was 12% in smooth tubes and 15% in dimpled tubes. The maximum deviation for the friction factor was 6.1% in smooth tubes and 8.3% in dimpled tubes. The numerical model accurately represented the full dimensions of a commercial heat exchanger. Grid independence tests were conducted using a three‐dimensional unstructured. To ensure accurate results, the study used a tetrahedral mesh and a Realizable k–ε turbulence model in its simulations. The findings revealed that corrugated tubes with various ring and dimple configurations dramatically enhanced heat transfer. Specifically, tubes with diameter rings, distance between rings, dimpled‐ring diameters, and distance between dimple rings achieved maximum enhancements of 45.5%, 35.009%, 67.95%, and 58.42%, respectively. Furthermore, dimpled tubes with different diameters and distances also outperformed smooth tubes, showing heat transfer increases of 42% and 38.8%. The optimized dimpled tube design offers a promising approach for improving heat exchanger performance while minimizing pressure drop. Future research can build upon these findings to further refine and optimize corrugated tube heat exchanger technology.
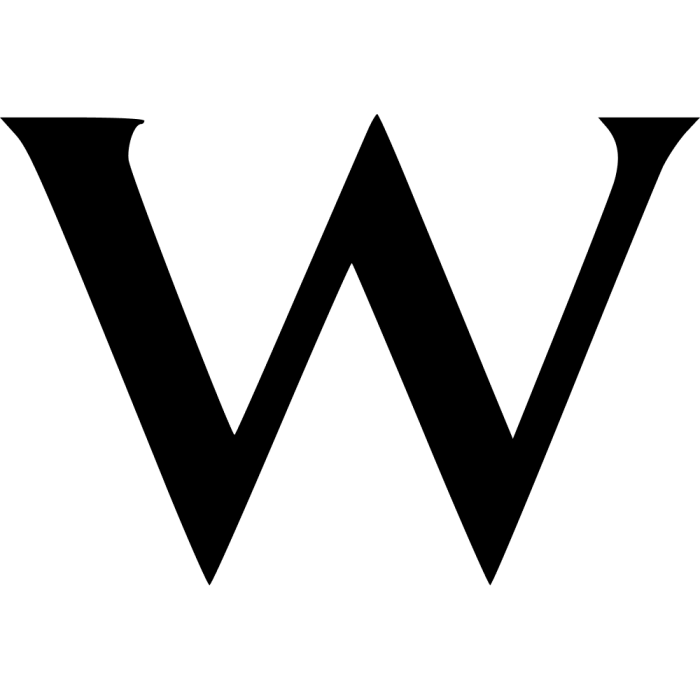
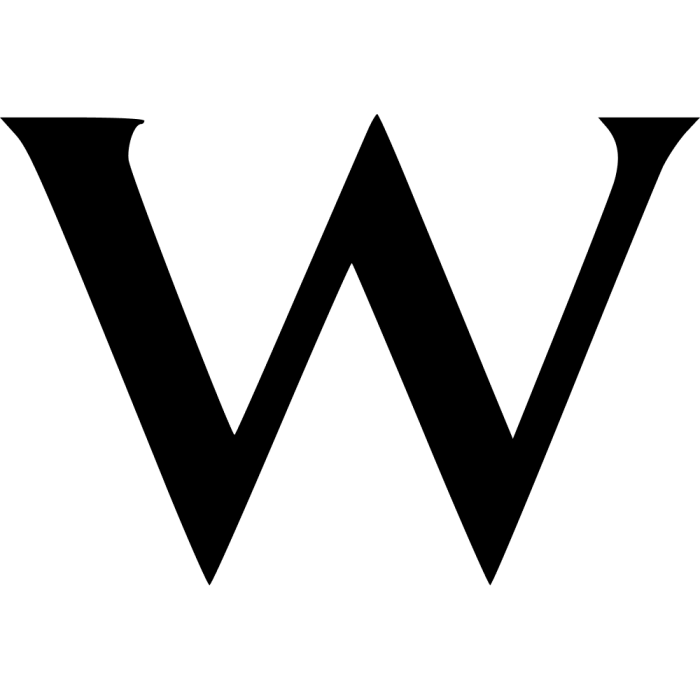
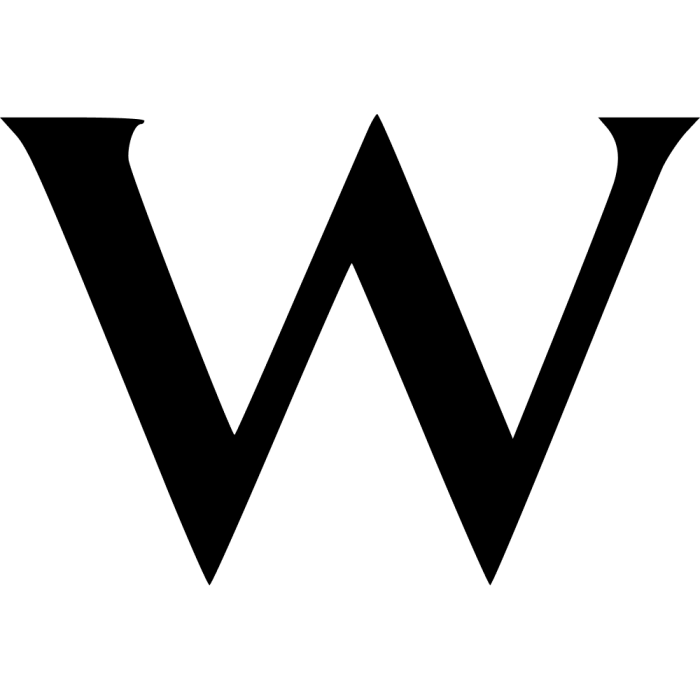
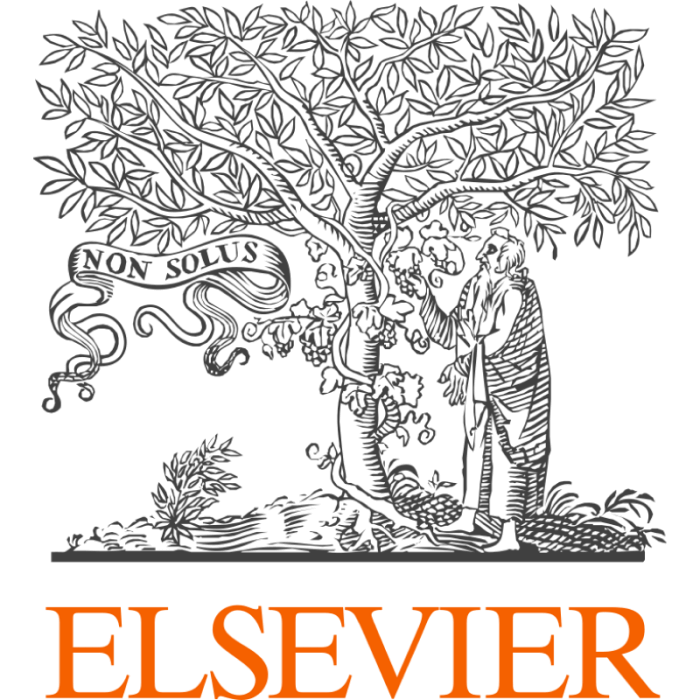
Nothing found, try to update filter.
Al‐Haidari S.R., Al‐Obaidi A.R.
ABSTRACTCorrugated pipe is used in many engineering applications because of its high performance compared with smooth pipe. This research involved numerical simulations and experimental testing of a circular tube with a modified flow path to improve the heat transfer performance of heat exchangers. The focus was on enhancing mixing and creating vortex flows within the tube to increase heat exchange efficiency. The impact of seven design factors, including ring diameters (RD) and the pitch between ring pitches (RP), on thermal–hydraulic performance was investigated. Water is used as the working fluid and the flow regime ranges from 4000 to 15,000, indicating turbulent flow. A constant heat flux of 25,500 W/m2 is applied, and the water enters the system at a temperature of 298 K (25°C). The properties of water are assumed to remain constant throughout the flow with flow conditions, such as a steady state (the flow conditions do not change with time), incompressible flow (the density of the fluid remains constant), and no‐slip condition (the fluid velocity at the surface of any solid boundary is zero). Corrugated tubes consistently outperformed smooth tubes in heat transfer due to increased flow mixing and separation. Both increasing the Reynolds number and decreasing the design factors led to the formation of mixing and vortex patterns. In RD configurations, the Nusselt number saw an average improvement of approximately 45.6%, while the friction factor increased between 19% and 57%. RP configurations demonstrated a broader range of Nusselt number enhancements, reaching up to 35%, and friction factor increases ranging from 15% to 42%. Rings can significantly enhance the thermal–hydraulic performance of tubes. However, the best configuration depends on the specific application. The configuration with the highest performance, resulting in a 1.38 increase in performance evaluation factor, was obtained using an RD of 1 mm and an RP of 20 mm. The simulated and experimental data showed excellent agreement, with a maximum discrepancy of less than 11% for both smooth and dimpled tubes.
Mohammed N.A., Khudhur D.S.
ABSTRACTIn this paper, the convective heat transfer (HT) and airflow characteristics are numerically examined for skewed wavy rectangular channels inserted partially with copper metal foam. Calculations were performed using ANSYS Fluent 19.2 at the airflow with a laminar range of Reynolds number from 700 to 1700. The thermohydraulic performance (THP), friction factor (f), and average Nusselt number (Nuavg) variation with Re for foam heights of hmf = 0.2–0.3H and foam pore densities of 10, 20, 30 and 40 pores per inch (PPI) have been examined for the tested channels. The results indicated that partial metal foam inserts enhance temperature distribution and increase the HT rate inside the channel due to the large HT surface area, high‐thermal conductivity of copper, and increased flow resistance, which increases the velocity of the fluid passing through the heat exchange system. Also, increasing hmf, PPI, and Re improves the HT rate in the channel, leading to an increase in both Nuavg and f due to decreased permeability. In addition, under constant hmf conditions, the THP exhibited a rise when the PPI and Re increased. Furthermore, at constant PPI and Re, the THP value lowers when the hmf grows due high increase in flow restriction. At hmf = 0.2H, 40 PPI, and Re = 1700, the THP reaches a maximum value of 1.51.
Al‐Haidari S.R., Al‐Obaidi A.R.
ABSTRACTIn the current work, the study examines the flow patterns and heat transfer capabilities of tubes with various spherical dimple configurations. A numerical analysis, supported by experimental validation on a reference model, was conducted on a circular tube with an alternating flow path. The primary goal was to enhance the thermal performance of circular tubes by inducing mixing and vortex flows. The impact of three design factors on thermal–hydraulic performance was investigated, dimple pipe diameter (DPD), dimple group number (DGN), and number of dimples (NODs). Dimpled tubes consistently outperformed smooth tubes in heat transfer due to increased flow mixing and separation. Both increasing the Reynolds number and decreasing the design factors led to the formation of mixing and vortex patterns. The performance evaluation factor (PEF) varied across different dimple configurations. For DPD, PEF ranged from 1.14 to 1.33; for DGN, it ranged from 1.15 to 1.28; for NOD, it ranged from 0.95 to 1.21, all within a Reynolds number range of 4000–15,000. At a Reynolds number of 6000, all three configurations of DPD, DGN, and NOD outperformed the smooth pipe in terms of the Nusselt number. For DPD, Nusselt number improvements ranged from 25.7% to 30.8%, and friction factors increased by 21% to 67%. DGN configurations exhibited a wider range of Nusselt number enhancement from 25% to 49.6%, and friction factor increase from 37% to 72%. NOD configurations also demonstrated consistent improvements, with Nusselt number increases ranging from 27.35% to 31% and friction factor increases from 42% to 74%. Spherical dimples can significantly enhance the thermal–hydraulic performance of tubes, so the best configuration depends on the specific application, and the highest performance, with a 1.33 increase in PEF, was achieved with a dimple diameter of 2 mm (DPD = 2 mm) and a dimple density of four dimples per unit area (NOD = 4).
Theeyzen S., Freegah B.
AbstractThe earlier studies investigated many parameters affecting the flat plate solar collectors (FPSCs) while employing an active approach to transmit the heat transfer fluid and running under a constant heat flux. In contrast, the presented study investigates enhancing the thermal performance through added fins with different heights and numbers to FPSC in a changing heat‐flux condition and relies on a passive technique. Thus, Models A, B, and C included adding five fins along the riser‐pipe with heights of 5, 7.5, and 10 mm, respectively, while Models D and E used four and three fins of 10 mm height, and the numerical calculations were conducted using ANSYS Fluent 2022R1. Then, the experimental work was done for the traditional model in Baghdad City, Iraq, to validate the results of numerical work, and the numerical and experimental work difference was found to be 10.17% for the tank's average temperature and the heat transfer liquid's temperature at the riser outlet is 10.14%. The numerical results indicate that the thermal efficiency of the system in all test models (A, B, C, D, and E) is enhanced than the classical model regarding the water's temperature in the tank and the working liquid's temperature at the pipe's outlet. In addition, the study concluded that Model C achieved a greater overall thermal efficiency than the traditional model by 38.59% and higher than Models A, B, D, and E by 11.77%, 6.65%, 8.19%, and 18.09%, respectively.
Mustafa A.J., Ghani I.A.
AbstractPassive heat transfer techniques in minichannel heat sinks (MCHS) provide effective thermal management solutions for high heat flux applications. The current study introduces a three‐dimensional numerical analysis conducted to explore the flow and heat transfer characteristics of MCHS utilizing two passive techniques: incorporating pin fins with oblong‐shaped cavities. Four types of pin fin shapes were developed, including tear‐drop (MCOC‐TDPF), pyramidal (MCOC‐PPF), conical (MCOC‐CPF), and oval (MCOC‐OPF), respectively. The study is carried out under a laminar flow regime with Reynolds number ranging from 100 to 1000. The overall performance of these designs is assessed through a comparative analysis of traditional MCHS based on average Nusselt number, friction factor, and overall performance factor. Among these designs, MCOC‐CPF exhibited superior thermal performance compared to the other three configurations, with a maximum performance factor of 2.25 at a Reynolds number of 1000. Furthermore, the influence of conical pin fin taper ratio (β) on the thermal enhancement of MCOC‐CPF is also analyzed. Four values of conical pin fin taper ratio (β) have been considered, namely 1/6, 1/3, 1/2, and 2/3. The results revealed that β = 1/3 achieved an optimal overall performance of 2.39 at Reynolds number Re = 1000.
Al‐Haidari S.R., Al‐Obaidi A.R.
AbstractEnhanced pipe surfaces offer greater heat transfer enhancement due to increased turbulence levels, leading to improved heat exchange performance. This study combines numerical simulations and experimental work to identify the best geometric design of enhanced tubes for thermal–hydraulic performance, flow structure, and pressure drop, and the simulations are validated with experimental data. Water is a working fluid with Reynolds numbers ranging from 4000 to 15,000, q = 25,500 W/m2, and an inlet temperature of 298 K with constant fluid property, steady state, and no‐slip condition. The three‐dimensional steady incompressible turbulent flow in the concavity dimpled shape‐enhanced tubes is numerically studied. This research found that pipes with a concave shape transfer heat most effectively. The overall heat transfer is significantly influenced by the shape of the dimples, their arrangement in rings, the size of these rings, and the number of rings. However, the number of cylindrical dimples does not seem to impact heat transfer much. The increase in heat transfer performance was by 9.8%–61% for dimple rings = 2ring performed best compared with a smooth pipe and by 8.21%–38.49% at the effect of ring numbers as grouping, also the dimple ring diameters by 5%–38% and by 7%–39% at dimple numbers. The performance evaluation factor (PEF) assesses overall performance by considering both the pressure drop penalty and improved heat transfer. The optimal configuration achieving the highest performance (PEF = 1.295) at a flow rate (Re) of 4000 involves a single dimple ring with a 2‐mm diameter, spaced 10‐mm apart, containing four dimples. Furthermore, discussing the different parameters of thermal and hydraulic performances to obtain the best thermal performance, and increasing the number and size of dimples gives a better guide for engineering to obtain better thermohydraulic performances for heat exchangers.
Sheikholeslami M., Abd Ali F.A.
New configuration of concentrated photovoltaic thermal (CPVT) with the implementation of parabolic concentrator and heat sink combined with the vortex generator (VG) were presented in current work. The testing fluid is water and temperature-dependent features were utilized. The regime of water flow in absence and presence of VG are laminar and turbulent, respectively. Numerical simulations were done for different values of angle of VG (θ = 30°, and 60°), pitch ratio (S = 0.025, 0.0375, and 0.05), and volumetric flow rate (Q = 0.5, to 2 Lit/min). Four values for width of reflector have been applied and radiation model was utilized to derive the absorbed heat flux. The accuracy of modeling has been examined for three cases and good accommodations have been reported. The maximum values of thermal (ηth) and electrical (ηel) performance are 63.75 % and 13.96 % which happens when θ = 30°, S = 0.025, Q = 2 Lit/min. Installing VG leads to increments of ηth and ηel about 1.42 % and 2.74 %. Increase of S and θ cause performance to decrease while this function increases with rise of Q. Increase of Q causes ηth and ηel to increase about 1.17 % and 2.55 % for the best case.
Sheikholeslami M., Ghasemian M., Dehghan M.
Al-Obaidi A.R.
In this work, numerical modeling techniques were used to determine the thermo-hydraulic flow behavior, heat transfer enhancement, and overall thermal performance of fluid moving inside a corrugated pipe with constant heat flux. The flow patterns, pressure drops, heat transfer coefficients, friction factors, Nusselt numbers, ratios of the Nusselt number to the friction factor, the friction factor for corrugated pipe in comparison with smooth pipe, and the thermal performance factors under various corrugated pipe geometry configurations and ranges of Re number were all predicted numerically. The distance between the corrugated rings of 5, 10, and 15 mm, the ring angles of 120, 240, and 360 degrees, and the diameter of the corrugated rings of 1, 2, and 3 were all modified by numerical calculations. The numerical findings unmistakably demonstrate that the pressure drop increased dramatically as the corrugated patterns took shape. The Nusselt numbers (Nu) values of the designs were about 32.2, 40.5, and 45.6% higher than those of the smooth pipe for a Re of 12,021.9. The smooth pipe’s Nu values were 17, 29, and 49.6% less than the value specifications. For the configuration, the Nu were, respectively, around 49.5, 45.7, and 40.9% higher. The results also show that the PEF performs best in the 1.2–1.6 range. Numerous correlation equations were created using Minitab, response surface methodology, and regression analysis for the friction factor (f), Nu, and PEF. These correlation equations' average errors were almost 13%, 9.75%, and 13.33%, respectively.
Total publications
6
Total citations
40
Citations per publication
6.67
Average publications per year
3
Average coauthors
1.17
Publications years
2024-2025 (2 years)
h-index
3
i10-index
3
m-index
1.5
o-index
7
g-index
6
w-index
1
Metrics description
h-index
A scientist has an h-index if h of his N publications are cited at least h times each, while the remaining (N - h) publications are cited no more than h times each.
i10-index
The number of the author's publications that received at least 10 links each.
m-index
The researcher's m-index is numerically equal to the ratio of his h-index to the number of years that have passed since the first publication.
o-index
The geometric mean of the h-index and the number of citations of the most cited article of the scientist.
g-index
For a given set of articles, sorted in descending order of the number of citations that these articles received, the g-index is the largest number such that the g most cited articles received (in total) at least g2 citations.
w-index
If w articles of a researcher have at least 10w citations each and other publications are less than 10(w+1) citations, then the researcher's w-index is equal to w.
Top-100
Journals
1
2
3
4
5
|
|
Heat Transfer
5 publications, 83.33%
|
|
International Journal of Heat and Fluid Flow
1 publication, 16.67%
|
|
1
2
3
4
5
|
Citing journals
2
4
6
8
10
12
14
16
|
|
Applied Thermal Engineering
16 citations, 32%
|
|
Heat Transfer
15 citations, 30%
|
|
Results in Engineering
14 citations, 28%
|
|
International Journal of Thermofluids
2 citations, 4%
|
|
International Journal of Heat and Fluid Flow
1 citation, 2%
|
|
International Communications in Heat and Mass Transfer
1 citation, 2%
|
|
Flow Measurement and Instrumentation
1 citation, 2%
|
|
2
4
6
8
10
12
14
16
|
Publishers
1
2
3
4
5
|
|
Wiley
5 publications, 83.33%
|
|
Elsevier
1 publication, 16.67%
|
|
1
2
3
4
5
|
Organizations from articles
1
2
3
|
|
Organization not defined
|
Organization not defined, 3, 50%
Organization not defined
3 publications, 50%
|
University of Baghdad
3 publications, 50%
|
|
1
2
3
|
Countries from articles
1
2
3
4
|
|
Iraq
|
Iraq, 4, 66.67%
Iraq
4 publications, 66.67%
|
Country not defined
|
Country not defined, 3, 50%
Country not defined
3 publications, 50%
|
1
2
3
4
|
Citing organizations
2
4
6
8
10
12
14
16
18
20
|
|
Organization not defined
|
Organization not defined, 19, 47.5%
Organization not defined
19 citations, 47.5%
|
University of Baghdad
2 citations, 5%
|
|
Al-Mustansiriyah University
1 citation, 2.5%
|
|
2
4
6
8
10
12
14
16
18
20
|
Citing countries
2
4
6
8
10
12
14
16
18
20
|
|
Country not defined
|
Country not defined, 19, 47.5%
Country not defined
19 citations, 47.5%
|
Iraq
|
Iraq, 4, 10%
Iraq
4 citations, 10%
|
2
4
6
8
10
12
14
16
18
20
|
- We do not take into account publications without a DOI.
- Statistics recalculated daily.